How to operate small sawdust pellet press?
Different small sawdust pellet press have different methods of operation, now let’s talk about how to operate it:
- Check that the screws are fastened before using the sawdust pellet press machine.
- Release the two adjustment screws on the two ends of the press wheel before starting, then start the motor to observe whether the drive is the same as the logo.
- New disc running-in: the small sawdust pellet press should be used for the first time, the method is as follows: take 5 kg raw material and 1 kg fine sand mix evenly, then add 1 kg waste oil to mix well. Start the machine, put in the raw material after leveling, adjust the roller bolt with the wrench, wait until the normal discharge (note: the adjustment gap can not be too small, or will damage the roller and grinding plate.) Keep the machine running for 1 hour before adding normal raw materials to production. If the raw material can not be normally granulated, press roller bolts should be slightly loosened until the normal discharge. After adjustment, the pellets can not be produced normally, and steel nails are used in the mould plate. The oil or dry material is penetrated (the steel nail grinds the head flat and then runs again. When the operator completes the day's pelletizing, after the raw material is pressed in the pellet press, the machine is added with oil (mixture of raw materials and 10% waste oil) to fill the die hole to ensure that the die hole is not blocked, so that the operator will be ready for the next operation. The next time the device starts will save a lot of time.
- Material requirements: material moisture should be adjusted to 14%-18%, high or too low water content will affect the yield and quality of the pellets; at the same time, the raw material should be mixed evenly and the moisture is consistent.
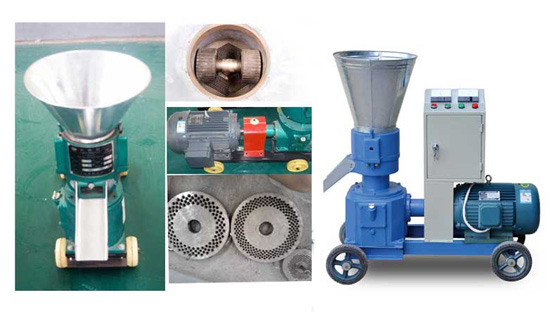
- In the use of small sawdust pellet press, the feed is stopped before stopping, and after the material is processed in the bin, the oily material is added into the template hole to keep the hole smooth, in case of the next use, the phenomenon of blockage will not occur.
- Under normal production conditions, the roller bearings must be cleaned once with gasoline or diesel oil once in five days, at the same time high speed lubricating oil is injected, gears are repaired and maintained half a year, and vertical shaft bearings are cleaned once every 7 days.
- Adjustment of the clearance of die disc pressing roller:
- The clearance between the roller and the die plate has a great influence on the pellet quality, and the general clearance should be between 0.05mm and 0.3 mm. When the gap is greater than 0.3 mm, the material layer is too thick and unevenly distributed, which reduces the pelletizing yield. When the gap is less than 0.05 mm, the machine wear is serious. The method of judging the distance between rollers and dies: it is generally good not to turn on the roll when it is turned on or to throw the material into the pellet press by hand. Adjustment method: adjust screw 8 with internal hexagonal wrench (spare parts).
- The selection of hole depth and pore diameter (compression ratio): the die plate with low pore depth and pore diameter ratio has high grain production but low hardness. Otherwise, the production is low and the hardness is high. Therefore, the user should choose according to the needs of different molds, when necessary to provide raw materials, we customized for you to meet your needs.
- Regulation of pellets length: adjust the length of pellet material by adjusting the cutting height of the edge of the outlet.
- The replacement method of the die plate: use a screwdriver to level a tooth with a gap in the nut on the main shaft stop washer, screw out the nut with the hook wrench (spare parts), take out the stop washer and the peace washer, and then remove the die plate with the die disc opener. After the replacement of the new die disc, according to the above method to re-run.
- Grain processing: the temperature of the processed pellets is higher, should be kept in a ventilated place cool to room temperature before bagging storage.
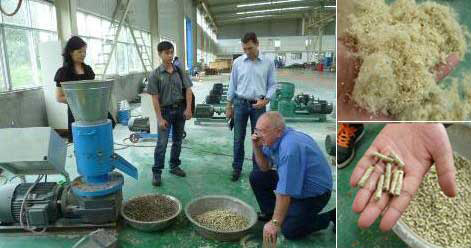